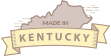
Articles
Learn about prefab cabins, portable garages, and sheds or get inspired for your own project!
Needing answers about shed homes? This article outlines the costs and building process of converting a shed into a home, while also giving other shed home ideas.
This article covers the nuances of tiny home regulations in Kentucky, providing information for specific KY city and county building codes for tiny homes.
Tiny houses are experiencing a surge in popularity, attributed to their attractive tax benefits, reduced utility expenses, and affordable purchase prices nationwide.
We understand your questions regarding tiny house shells. In this article, we explain the sizes, costs, styles, and steps to customizing your tiny house shell.
If you’re wondering about the properties of vinyl siding and its suitability for use in vinyl siding for shed storage and garages, as well as the cost, benefits, and durability of vinyl storage, you’ve come to the right place. Please read this article carefully as it provides answers to these questions and more.
Looking to boost your shed’s natural light and space? Consider adding a dormer for enhanced appearance and increased natural light & roominess!
Need some inspiration and visuals for your shed porch? Here are some styles, designs, and ideas to get you rolling and inspire ideas of your own.
Not sure what shed permit regulations apply to you in TN? This article should simplify the guidelines and help you understand how Tennessee building codes work, especially with shed permits.
Golf carts are becoming increasingly popular as a transportation method at golf clubs, amusement parks, airports, and even residential areas. Golf carts offer a convenient, low-cost alternative to cars and trucks; however, they need a secure place to be stored when not in use. That is where golf cart garages come in.
Not sure what the building permits are like for where you live in KY? Here’s a comprehensive list of town/cities all over KY that might answer your questions!